It has been a constant battle since we moved, to grade the area around our barn so that the water runs away from, and not into the barn. The underlying problem is that some moron built the barn at the LOWEST place at the BOTTOM of a hill. Since the barn is at the LOWEST place at the base of the hill, grading the ground away from the barn is very difficult. I have finished one side of the barn after two days of work. Most of the work was done with the blade on the tractor, but there was still a large portion of the work that had to be done by hand. I used some small logs to make a retaining wall that helps deflect water as well as several other alterations to the ground around the barn.
This is pretty much an overview of this entire side of the barn/shop.
Here is the retaining wall.
I was experimenting with a new blacksmith technique the other day. I was using a short v-shaped slot punch, to slit a hole in a bar of metal. Since I was using a short punch, I was using a pair of tongs to hold the punch. Well, I messed up my hammer blow and hit the punch at an angle. This propelled the punch outside of the shop.......uhhh THROUGH my window. The hole in the metal didn't turn out that great but I've got a nice hole in my window!
I've begun work on stock items for craft shows. I have made 63 J-hooks so far, and I am hoping to do 30 dinner bells tomorrow.
Also, on the "to-do" list is a retaining wall and grading job on the other side of the barn. That will be a LOT more work as there will be at least twice the amount of dirt to move. Never a dull moment!
Me blog about meself! Ramblings of blacksmithing, sailing, and my general work around my place!
BE SURE TO CHECK OUT MY BLOG PAGES IN THE WHITE LINKS ABOVE!!!
Wednesday, March 28, 2012
Friday, March 23, 2012
Intensive Blacksmithing Instruction in Mississippi
Well folks, last week I took my first ever trip away from home. It lasted nine days. I went to Brandon, Mississippi for seven days of one-on-one blacksmithing instruction with blacksmith Brian Brazeal. Instead of driving, I took a Greyhound Bus from Bowling Green, Kentucky to Jackson, Mississipi. I'm not going to say anything about anyone, but suffice to say, a LOT of weird people ride Greyhound busses. Ok so yeah I know, I'M weird, but I'm talking about a whole different array of weird. So anyway, I didn't get to take a lot of pictures, but Brian's assistant Lyle, did. He has a much better camera than I do, so his pictures are better anyway.
Starting out, here are a few pictures I took to start the trip out with.
First, the Bowling Green bus station.
Awaiting the arrival of my bus!
I had a transfer in Nashville! These pictures were taken just after I boarded the bus in Nashville.
BIRMINGHAM Alabama!
The sunset in Mississippi was great.....kind of hard to catch at 70 MPH, but you get the idea!
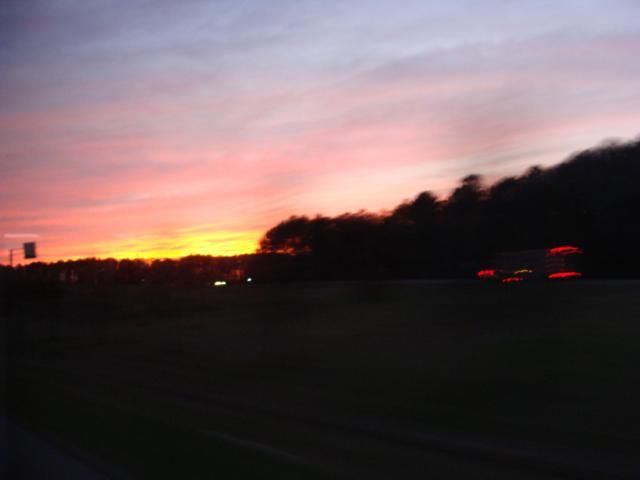
Lyle came over on day one of class, and took quite a few pictures. The first thing we made was a hot cut hardy. I swung a large sledge hammer while Brian directed the hits and held the tooling.
More pictures of that tool later.....for now we have to let it cool!
The next thing was to make my own hammer. Once again, Brian directed and held the tooling, while I swung the sledge hammer.
First thing to do was mark the location of the hole.
Then we start punching the hole!
Here is the hole about half way done!
Next we finish punching the hole. This part of the process requires the punch to be cooled. The coolant (beeswax) is flamable and the metal is hot. Which means that when the punch is struck a ball of flame is forced out of the hole. If you have a good camera, it's a pretty neat thing!
Next, the hole is sized and shaped using a drift.
Sometimes it's good to stretch out a bit! Or uhhhh actually just swing REALLY hard!
The starting piece of steel and the hammer......so far! No, we aren't done yet!
Next the hammer is shaped.
And NOW it is starting to look like a hammer!
The hammer is then heated, and cooled rapidly to harden it. We then heated up one of the drifts and used that to temper the hammer head.
Learning as much as I can and enjoying every minute of it!
Why make a hammer if you aren't going to make the wedge too?
The hammer, handle, wooden wedge, and steel wedge.
The hardies we made earlier and the hammer head.
Making a flower!
On another day of class, Brian and I forged a large grape leaf candle holder. It was forged from 1-inch solid square bar. Here is Brian working on part of it.
Here I am forging out the candle holder side of it.
On the last day of class, Brian and I decided to forge a larger hammer. The hammer we made on the first day of class was a 3 pounder. So we decided to do a 4.5 pounder. This time Brian did the striking and I held the tooling.
Here I am about a millisecond away from dropping this piece on the ground and fumbling around with it. (No, I don't have the coordination that Brian has! :D)
Brian marking the center!
Really good fireball pictures!
Drifting and shaping the hole.
Fumbling with the metal.....again!
Shaping things up!
The original blank and the hammer so far!
Continuing to shape the hammer!
Finishing up!
I see a hammer!
From left to right.....the starting blank, my hammer, and Brian's hammer.
Polishing the hammer!
Heating the hammer faces so that they can be hardened.
Plunging the hammer head into water to harden it as fast as possible.
The same technique of heating a drift was used to temper this hammer.
Tradition says that a student is supposed to forge a special nail to go in the teacher's nail stump. I forged a D-shaped nail (for my first initial.)
After seven days of class we had forged quite a bit of tools and pieces. Here they all are.
Putting my nail in the nail stump with Brian!
Here is a copper leaf I forged! Copper is fun!
Here is one of the hardies in my anvil.
Here is the big hammer we forged.
And here are a lot of the tools we forged, on my tool rack!
Now all I have to do is put all of this new knowledge to use!
Starting out, here are a few pictures I took to start the trip out with.
First, the Bowling Green bus station.
Awaiting the arrival of my bus!
I had a transfer in Nashville! These pictures were taken just after I boarded the bus in Nashville.
BIRMINGHAM Alabama!
The sunset in Mississippi was great.....kind of hard to catch at 70 MPH, but you get the idea!
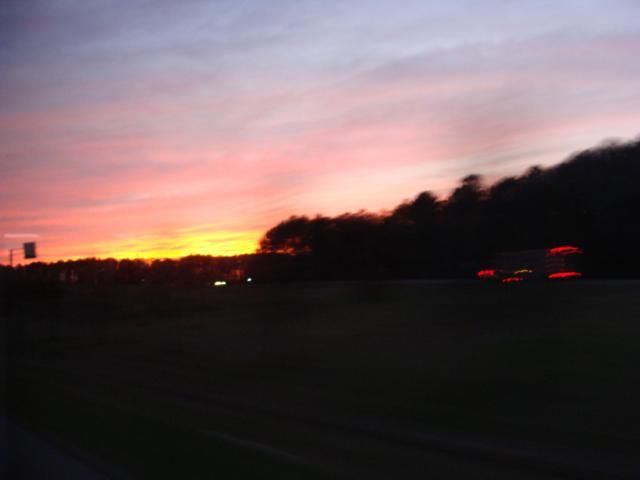
Lyle came over on day one of class, and took quite a few pictures. The first thing we made was a hot cut hardy. I swung a large sledge hammer while Brian directed the hits and held the tooling.
More pictures of that tool later.....for now we have to let it cool!
The next thing was to make my own hammer. Once again, Brian directed and held the tooling, while I swung the sledge hammer.
First thing to do was mark the location of the hole.
Then we start punching the hole!
Here is the hole about half way done!
Next we finish punching the hole. This part of the process requires the punch to be cooled. The coolant (beeswax) is flamable and the metal is hot. Which means that when the punch is struck a ball of flame is forced out of the hole. If you have a good camera, it's a pretty neat thing!
Next, the hole is sized and shaped using a drift.
We begin forging the hammer face.
Sometimes it's good to stretch out a bit! Or uhhhh actually just swing REALLY hard!
The starting piece of steel and the hammer......so far! No, we aren't done yet!
Next the hammer is shaped.
And NOW it is starting to look like a hammer!
The hammer is then heated, and cooled rapidly to harden it. We then heated up one of the drifts and used that to temper the hammer head.
Learning as much as I can and enjoying every minute of it!
Why make a hammer if you aren't going to make the wedge too?
The hammer, handle, wooden wedge, and steel wedge.
The hardies we made earlier and the hammer head.
Making a flower!
On another day of class, Brian and I forged a large grape leaf candle holder. It was forged from 1-inch solid square bar. Here is Brian working on part of it.
Here I am forging out the candle holder side of it.
On the last day of class, Brian and I decided to forge a larger hammer. The hammer we made on the first day of class was a 3 pounder. So we decided to do a 4.5 pounder. This time Brian did the striking and I held the tooling.
Here I am about a millisecond away from dropping this piece on the ground and fumbling around with it. (No, I don't have the coordination that Brian has! :D)
Brian marking the center!
Making a gentle mark to establish the hole.
Hammering in earnest!
Really good fireball pictures!
Drifting and shaping the hole.
Forging the face!
Fumbling with the metal.....again!
Shaping things up!
The original blank and the hammer so far!
Continuing to shape the hammer!
Finishing up!
I see a hammer!
From left to right.....the starting blank, my hammer, and Brian's hammer.
Polishing the hammer!
Heating the hammer faces so that they can be hardened.
Plunging the hammer head into water to harden it as fast as possible.
The same technique of heating a drift was used to temper this hammer.
Tradition says that a student is supposed to forge a special nail to go in the teacher's nail stump. I forged a D-shaped nail (for my first initial.)
After seven days of class we had forged quite a bit of tools and pieces. Here they all are.
Putting my nail in the nail stump with Brian!
Here is a copper leaf I forged! Copper is fun!
Here is one of the hardies in my anvil.
Here is the big hammer we forged.
And here are a lot of the tools we forged, on my tool rack!
Now all I have to do is put all of this new knowledge to use!
Subscribe to:
Posts (Atom)